8 Ways Big Data Analytics Is Improving Logistics
Table of Contents
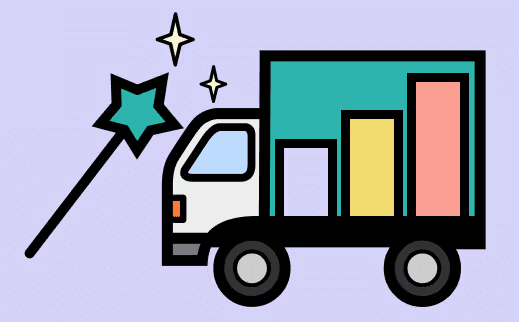
Logistics has never been more complex than it is today. The global nature of the supply chain has created constantly shifting dynamics that can significantly impact a company’s profitability.
In response, data analytics is helping manufacturers, shippers, and retailers gain visibility into their operations and optimize them so they can better deal with the unexpected. As a result, data-driven companies are increasing profit margins and customer satisfaction levels. Let’s look at eight specific ways that data analytics is improving logistics.
1. More accurate supply and demand forecasting
Using the wealth of proprietary and third-party data available, companies can track and adapt to shifts in demand in near real-time. Big data analytics allows companies to generate more accurate supply and demand forecasts to inform inventory and shipment planning. As a result, they can reduce waste and improve delivery times. While “black swan” events will remain impossible to predict, critical insights from data allow companies to adapt their logistics to these events more quickly.
Sigma pro tip: See how Accenture helped a national food distributor improve forecasting accuracy and inventory management by integrating internal and external data.
2. Inventory management
If a product is out of stock, there’s a high likelihood that shoppers will shift their purchase behavior. An IHL study revealed that 37% of customers who encounter an out-of-stock item will purchase from a different brand, while 21% will buy from a different retailer. Overstocking causes problems as well. Money is wasted through unnecessary storage costs, personnel costs, and loss of product due to expiration.
To avoid these issues, companies can use data to calculate logistics lead times for each SKU and determine the number of days it typically takes products to reach the warehouse after submitting a purchase order. Combining these lead times with sales data will help identify reorder points for each item to prevent stockouts.
Sigma pro tip: See how Clover improved inventory management with data-driven insights.
3. Warehouse management
In addition to reducing stockouts and overstocks by optimizing inventory management, data analytics can also improve the efficiency of warehouse management. Companies can track the movement and location of stock and combine this information with sales data to identify the best location for each SKU in the warehouse and find opportunities to streamline.
Sigma pro tip: See how a leading logistics company used warehouse management system data to improve order fulfillment and streamline operations.
4. Supplier risk management
To improve their operations, companies should identify risks associated with their suppliers. With this information, companies can either work with their suppliers to solve the problems creating the risks or select new suppliers if the risks can’t be mitigated (i.e. incidents of natural disasters or political instability that affect the supplier’s ability to fulfill commitments).
To improve supplier risk management, companies can track any indicator that reflects a risk, such as:
- Late shipments
- Delivery to the wrong location
- Delivery of the wrong product or quantity of product
- Inefficient processes used by suppliers
- Regulatory compliance issues
Sigma pro tip: See how a Fortune 500 food wholesaler improved vendor performance using supply chain data analytics.
5. Route optimization
Due to cost reduction initiatives and sustainability efforts, many logistics companies are seeking ways to optimize routes. GPS data, road condition data, and weather data can be combined with fleet data to identify the best route for each vehicle at any given time. Companies can define which route is best based on a variety of different factors, including traffic, travel time, and fuel efficiency. Additionally, the value of this data increases as more of it accumulates, since route data and driving history data can be mined for patterns and trends over time.
Sigma pro tip: See how Transvalair cut delivery times and improved service levels using SmartRoutes’ route optimization technology.
6. Performance management
Resources of both the human and mechanical sort perform best when they’re managed and maintained optimally. Supply chain data analytics can help companies understand the performance of their workforce and identify inefficient processes and workflows as well as ideal schedules for breaks. Sensors on company equipment automatically send performance and maintenance data, so managers can prevent bottlenecks due to downtime.
Sigma pro tip: See how organizations applied the SCOR model to identify performance gaps and improve decision-making across their supply chains.
7. Maintaining perishable product integrity
Many products are perishable, and shippers must ensure they arrive at their destination with their quality intact. If these items encounter temperatures or humidity levels outside their ideal range for an extended period of time, customers will be unhappy with the products (or even become sick, in the case of food and beverage products). Using data generated from sensors, companies can monitor the conditions that any given shipment encounters during its journey.
Sigma pro tip: See how Fictiv improved manufacturing and shipping tracking with data analytics.
8. Increased customer satisfaction
Customers want to know when they will receive their orders and if a package is expected to arrive later than anticipated. The more informed a customer is, the happier they tend to be. It’s now possible to offer real or near-real-time status updates, and companies that make it easy for customers to access these logistics updates will win in customer satisfaction.
And shipment tracking isn’t the only way that data can raise customer happiness. As more companies turn to automated customer support options, it’s crucial that they accurately analyze customer interactions. Data analytics can ensure customers connect with support efficiently and that they get solutions quickly. Additionally, companies can monitor customer feedback and identify areas where improvement is needed, as well as flag problematic interactions for supervisor-level assistance.
Sigma pro tip: See how SEKO Logistics used temperature-controlled shipping and real-time monitoring to protect perishable goods in transit.
Analytics: The advantage logistics teams need
As supply chain complexity grows and customer expectations rise, manufacturers, shippers, and retailers are rethinking their operations. Data analytics is already central to smarter logistics, and its role will only expand.
The companies moving fastest are the ones acting on insights, not just gathering reports. They’re using data to refine delivery routes, respond to supplier disruptions, and reorganize warehouse layouts with purpose. The earlier you start, the sooner you’ll see real results.
Let’s Sigma together! Schedule a demo today.