Predictive Analytics In Supply Chains: Beyond Basic Forecasting
Table of Contents
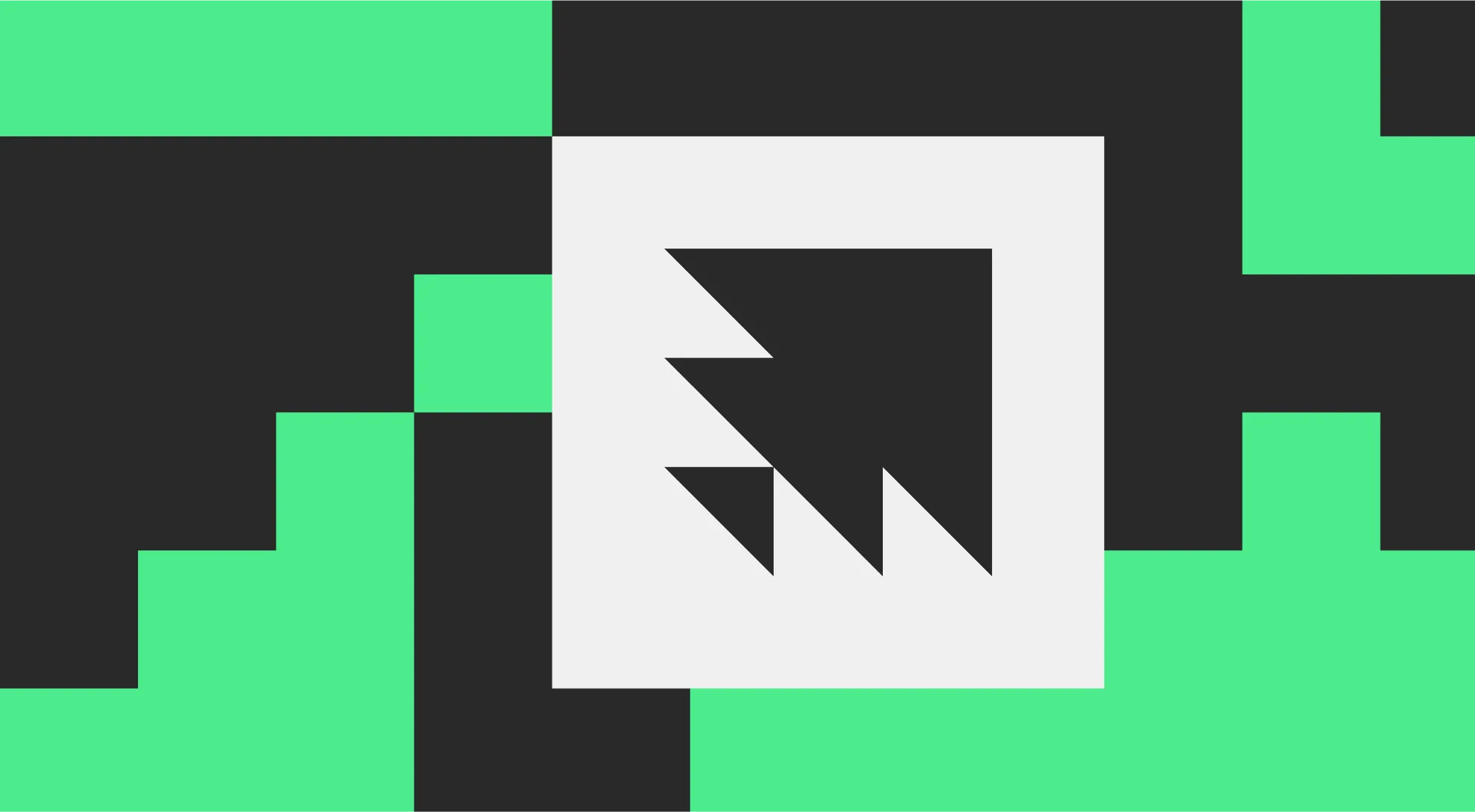
Key Takeaways:
- Advanced analytics is transforming supply chain operations. Moving beyond traditional forecasting, modern analytics tools give organizations deeper insights into supply chain trends and risks.
- Predictive analytics offers proactive risk management. Companies can anticipate disruptions like supply shortages or transportation delays and adjust plans in real-time for more resilient operations.
- Data integration enables smarter decision-making. Leveraging internal and external data, supply chain leaders can make faster, more accurate decisions that drive efficiency and reduce costs.
Imagine a global manufacturer struggling to keep up with fluctuating demand for a popular product line. Inventory surpluses build up in one region while another faces shortages, frustrating customers and impacting revenue. Traditional, excel-based forecasting models, once the backbone of planning, fall short, missing critical signals from the market. It’s a common story showing the limitations of relying solely on historical data.
Moving past basic forecasting, advanced techniques like machine learning and real-time data integration enable organizations to respond faster and more accurately to supply chain challenges. This evolution goes beyond predicting demand — it reshapes how supply chain leaders manage everything from production planning to inventory management to supplier risk mitigation.
Adopting these advanced methods is a strategic advantage for data-driven organizations, driving efficiency and resilience in modern supply chain operations.
The evolution of supply chain analytics
As supply chains have grown more complex, the need for robust analytics has evolved significantly. Traditional approaches, relying mostly on historical data, offered companies a look at past trends but restricted their ability to predict future disruptions or changes in demand. Today, with advances in machine learning and AI, supply chain analytics has transformed, allowing for a more proactive and dynamic approach.
One major change has been the shift to real-time data. Instead of waiting for monthly reports, supply chain leaders can access up-to-the-minute insights, enabling quicker responses to issues as they arise. This real-time capability also makes it possible to integrate external data sources (weather patterns, market trends, and even geopolitical news) that impact the supply chain in ways that historical data alone could never.
The COVID-19 pandemic that started in 2020 shone a bright light on these needs, and disruptions across supply chains underscored the importance of adaptive and resilient systems. Since then, companies have accelerated their adoption of predictive analytics to better prepare for uncertainties, setting a new standard for the industry.
Today’s supply chain analytics isn’t just about forecasting; it’s about understanding, adapting, and responding to real-world conditions in real-time, with all the data that matters.
Advanced supply chain forecasting techniques
Supply chain forecasting has evolved into a sophisticated discipline, leveraging advanced techniques to provide actionable, precise predictions. Below are key methods that are redefining how businesses forecast.
Machine learning models
Machine learning excels at uncovering patterns in massive datasets. For example, simple regression models can analyze seasonal sales trends, while more advanced neural networks detect hidden relationships in complex supply chain behaviors.
Some organizations take it further, applying natural language processing (NLP) to analyze news headlines or social media chatter to predict shifts in demand. These insights allow businesses to prepare inventory and production well before trends emerge.
Probabilistic forecasting
Instead of predicting one outcome, probabilistic models show a range of possibilities. Bayesian methods refine forecasts as new data becomes available, offering an adaptable approach for uncertain situations.
Monte Carlo simulations, on the other hand, help businesses model scenarios like sudden demand spikes or supplier delays, giving teams a broader understanding of what might happen and how to plan accordingly.
Hybrid forecasting systems
No single model fits every scenario. That’s where hybrid systems shine. By combining traditional forecasting methods with machine learning and probabilistic approaches, companies gain a more comprehensive view of potential outcomes.
For example, a retailer might use a hybrid system to predict both short-term holiday demand and long-term stock needs, ensuring flexibility across timeframes.
Supply chain demand sensing and real-time analytics
Real-time analytics is changing how businesses sense and respond to demand, replacing static reports with immediate insights that drive agility. For example, integrating real-time point-of-sale data allows companies to reorder top-selling items before shelves run empty, avoiding both stockouts and overstock. This dynamic approach ensures inventory aligns with actual demand, boosting customer satisfaction and profitability.
External data sources add even greater depth to this process. Social media, for instance, provides valuable clues about shifting market sentiment. A surge in online discussions about a product can alert supply chain teams to prepare for a potential spike in demand.
Similarly, weather patterns and economic indicators often dictate purchasing behavior—think of a sudden cold snap driving demand for winter apparel. Combining these insights with short-term trend analysis, like the impact of a recent promotion, empowers businesses to make quick, informed decisions and adapt to market changes in real-time.
How analytics paves the way for inventory optimization 2.0
Inventory optimization has become smarter and more strategic with the help of advanced analytics. Gone are the days of static stock levels and guesswork. Instead, companies now use real-time data and predictive models to ensure inventory is in the right place at the right time, without overloading warehouses or running into shortages.
One breakthrough is network optimization, which looks at inventory across the entire supply chain rather than in isolated locations. For example, companies can redeploy products to high-demand regions instead of holding surplus stock in multiple warehouses, reducing excess while maintaining availability where it matters most. Similarly, dynamic safety stock models adapt buffer levels to real-time conditions, ensuring businesses are ready for demand spikes without holding unnecessary inventory.
Managing long-tail products with low but steady demand has also become more efficient. By analyzing buying patterns, customer preferences, and regional trends, companies can identify opportunities to clear out these items. Seasonal or promotional campaigns targeted at specific audiences can free up storage and reduce holding costs.
Automation takes this a step further. Predictive analytics-powered systems automatically reorder stock based on demand patterns, lead times, and seasonal trends, reducing manual intervention while keeping inventory in sync with market needs.
Supply chain risk prediction and mitigation through better data analytics
Managing supply chain risk has always been complex, but with advanced analytics, organizations take a more proactive approach to predicting and mitigating disruptions.
By leveraging both internal and third-party data sources, you gain a comprehensive view of potential risks and can make informed decisions to safeguard operations in the following ways:
- Supplier risk assessment: By analyzing supplier performance metrics like delivery reliability and quality ratings, companies can identify potential weak points and evaluate the risk of relying on certain vendors. Some organizations also integrate financial data to assess a supplier’s economic health, providing a more complete picture of risk.
- Transportation network risks: Transportation delays can quickly disrupt the supply chain. Modern analytics platforms allow companies to track transportation performance, monitor route efficiency, and identify potential issues before they escalate. For instance, by analyzing historical and real-time data, companies can anticipate bottlenecks or delays and adjust routing to minimize disruptions.
- Geopolitical impact analysis: Global events, from trade restrictions to political conflicts, can have a major impact on supply chains. Analytics tools help companies stay informed of geopolitical trends, incorporating this data into their risk assessments and developing contingency plans to minimize risk.
- Weather-related disruptions: Weather events often disrupt logistics networks. Integrating weather forecasts and historical weather data into predictive models allows companies to prepare for potential disruptions in advance. For example, if a major storm is predicted along a shipping route, companies can reroute shipments or adjust the shipping method to avoid delays.
- Market volatility prediction. Market conditions fluctuate rapidly, affecting everything from raw material prices to customer demand. Modeling these fluctuations provides insight into potential supply chain volatility. With predictive insights, leaders can adjust sourcing, pricing, or stock levels, reducing the financial impact of market changes.
The possibilities of supply chain advanced data integration
The power of supply chain analytics grows exponentially when diverse data sources are integrated into a unified framework. By combining internal systems with external insights, businesses can unlock new levels of efficiency and adaptability.
Internet of Things (IoT) sensors are a key piece of this puzzle. From tracking the temperature of perishable goods to monitoring truck locations, IoT devices provide real-time data that helps prevent product losses and improve delivery timelines. For example, sensors can alert teams when temperature-sensitive items, like vaccines, are at risk, enabling immediate intervention.
Seamless data sharing is equally important. Application Programming Interfaces (APIs) connect suppliers, logistics providers, and other partners, allowing for near-instantaneous updates across the supply chain. Imagine a digital supply chain where production, shipping, and inventory systems all communicate in real-time. The result? Faster decisions, fewer bottlenecks, and a supply chain that operates as a cohesive unit.
Finally, real-time data processing ensures businesses act on insights as they arrive. Whether adjusting inventory to meet demand or rerouting shipments due to a weather disruption, having the ability to process and respond to data in real time keeps operations efficient and responsive.
Supply chain industry applications
Advanced analytics is reshaping supply chains across industries, offering tailored solutions to unique challenges. From retail to high-tech, here’s how different sectors are putting data to work.
Retailers often face unpredictable demand driven by trends, promotions, and seasons. By analyzing point-of-sale data and social media activity, they can adjust stock levels to meet demand. For instance, a fashion retailer might predict a surge in sales for specific items during a holiday sale, ensuring popular products are available while minimizing overstock.
Manufacturers, on the other hand, grapple with complex supplier networks. Predictive analytics allows them to assess supplier reliability and anticipate delays. A car manufacturer, for example, might monitor its suppliers’ performance and adjust orders based on anticipated production bottlenecks, avoiding costly downtime.
In the pharmaceutical industry, maintaining quality and compliance is critical. IoT sensors help track temperature-sensitive shipments, ensuring products like vaccines remain safe during transit. Analytics also aids in demand forecasting for medications, enabling companies to avoid shortages that impact patient care.
Food and beverage companies rely on analytics to manage perishable goods efficiently. Combining weather forecasts with demand data, a beverage company can prepare for a heatwave by ramping up production of cold drinks, ensuring shelves are stocked without excessive waste.
Tech companies operate global supply chains where components are manufactured in multiple regions. Predictive analytics helps coordinate production schedules and mitigate risks. For example, a smartphone manufacturer might analyze transportation and geopolitical risks to ensure timely delivery of critical parts, keeping product launches on track.
What’s next for supply chain analytics?
The future of supply chain analytics promises even greater possibilities, driven by emerging technologies and evolving priorities. Advanced methods, like AI and machine learning, are shaping a new era where supply chains become smarter, faster, and more sustainable.
AI is set to play a transformative role, powering autonomous supply chain systems where ordering, production, and distribution operate seamlessly based on real-time insights. Imagine a system that automatically adjusts production schedules to meet fluctuating demand or reroutes shipments in response to weather disruptions — all without human intervention. These innovations aren’t just improving efficiency; they’re redefining the limits of what’s possible.
Sustainability is also taking center stage. Companies are increasingly leveraging analytics to track emissions, optimize resource use, and meet environmental goals. For example, by analyzing transportation routes, businesses can reduce fuel consumption while ensuring timely deliveries, aligning profit with planet-friendly practices.
To successfully adopt these advancements, companies need a clear roadmap. Many start small, piloting analytics in specific areas like inventory management before scaling across the entire supply chain. Building strong foundations in data governance, cross-functional collaboration, and cloud infrastructure ensures these efforts are scalable and aligned with business goals.
As supply chain analytics evolves, one thing is clear: businesses that invest in these technologies today are setting themselves up for resilience and competitiveness tomorrow.
Supply chain predictive analytics frequently asked questions
How do we select the right predictive models for our supply chain?
Start with defining your specific requirements. For complex, non-linear patterns, machine learning models like neural networks can work well. Simpler models suit straightforward forecasting, such as linear regression. Pilot projects help test and refine what fits best.
How do we integrate multiple supply chain data sources effectively?
A clear data strategy is vital. Focus on identifying critical data sources and ensuring compatibility. Tools like APIs or cloud platforms simplify integration and enable real-time insights.
How do we handle supply chain data gaps and anomalies?
Use techniques like data cleansing, interpolation, and anomaly detection algorithms. Regular audits of your data sources also help maintain accuracy.
What specific risk mitigation strategies are essential?
Supplier assessments, transportation route planning, and scenario modeling are vital. Combine internal data with third-party insights to build robust contingency plans and keep operations resilient.