Sigma’s Hyegin Cho on Logistics Analytics and Supply Chain Optimization
Table of Contents
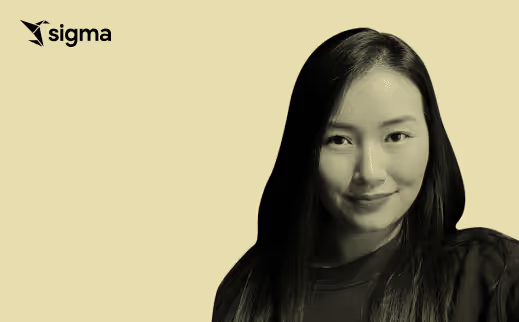
My name is Hyegin Cho, and for the past four years, I've been a logistics optimization analyst. But, after joining Sigma, I felt the need to voice my opinion on how Sigma would have solved the issues my logistics team and I faced every day.
This blog will cover the importance of logistics analytics and how they impact supply chains. We will learn why having a self-service BI tool can save organizations time, resources, and enable them to focus on driving the business forward.
What is Logistics Analytics?
Logistics analytics refers to organizations conducting analytical procedures to coordinate the logistical function throughout the supply chain. This is done to ensure operations are timely and efficient. Big data and business intelligence play a massive role in the logistics industry as these can both be leveraged to save an organization time and money.
In an industry where competitive advantages are crucial with demanding customers, understanding your logistics data will differentiate you from the pack and positively impact your everyday business operations. With logistics analytics tools you can take full control of your organization.
How Logistics Analytics Impacts Supply Chains
Logistics analytics can help optimize business processes and the supply chain to create more value while keeping operational costs low. By leveraging logistics analytics businesses can make data-driven decisions giving them a competitive advantage.
Take advantage of powerful logistics analytics and turn your logistics data into actionable insights to improve your supply chain.
- Conduct a detailed cost-benefit analysis to increase your profitability
- Increase operational capacity planning and simplify your supply chain.
- Optimize deliveries to ensure customer satisfaction
- Use real-time data to make critical business decisions
- Leverage logistics data to estimate future bottlenecks and unexpected issues based on predictive analytics
My Time as a Logistics Optimization Analyst
When I worked as a logistics data analyst on-site at a big tech company, my job was to build dashboards for our customers and internal managers to ensure that shipments were on time. Fresh data for logistics managers was critical for supply chain optimization since it allowed them to take quick action on any issue, minimizing negative impact.
I’ll highlight some of the major issues we faced and why we were overwhelmed by ad hoc requests. We were not properly equipped with the right tools to turn data into actionable insights. We needed a tool to allow our non-technical users to answer their own questions.
Need for Live Data for In-Transit Shipments
Transportation organizations have teams across every timezone: Europe, Asia, and the Americas because they wanted to make sure the shipments were being monitored at all times.
However, there weren’t any data analysts in those regions, so I had to support all regions.
If the in-transit shipment is expensive or a critical shipment, transportation team members wanted to be notified right away so that they can minimize delays.
Some shipments would be so time-sensitive that if they did not deliver on time, it was no longer useful for the project anymore. This often caused me to work late nights since the tools we used did not have functionalities to get to row-level detail for live data.
Limited Resources and Tools
Hiring a data analyst was difficult. We initially used Tableau and Data Studio + Google Sheets which did not serve us to the fullest. Since these tools were not meant to be used for deep data exploration, I often had to create a hacky way to achieve what they wanted.
End-users always came back to me for more data. This really slowed down any projects I had. I utilized App Script to dump data from Big Query to Google Sheets. I would create a hyperlink on Data Studio to lead them to Google sheets that had automated data pull. However, this often failed since Google sheets have small cell limits.
In reality, I needed all my data to be in one place so that I didn’t have to use multiple tools and extract data which was time-consuming and risky.
Root Cause Analysis for Delivered Shipments
Another way the team used the data was to find out what the delivery performance was and what were the root causes if the delivery performance did not meet the expectations. The dashboards I created showed high-level metrics for the team, but the managers wanted to see data underneath so that they can see exactly what caused delays.
They used this data to figure out the best way to fix the root cause of these delays. The problem was that any time they wanted this data, they had to reach out to me to get it. The canned dashboards could never fulfill their needs and the questions they had were always different requiring me to write custom SQL to pull the data for them.
QBR Time
When QBRs arrived, it was a nightmare. Every manager wanted their data for their portion of the presentation, but there weren’t enough data analysts to do the data crunching. Even though dashboards were already created for QBR presentations, there were so many outliers and bad data that needed attention.
Every manager wanted data pulls just different enough from the ones that are showing on the dashboards. I knew what the QBR metrics would consist of, so I tried to make dashboards as comprehensive as possible but every quarter, there were tons of ad hoc report requests that the dashboard could not answer.
Never Ending Ad Hoc Data Requests
The vicious cycle was always there. Managers would come to me for ad hoc requests. Then, my manager would tell me to turn it into a dashboard so that it can be more self-serving. However, no matter how many dashboards I created, these ad hoc requests did not end. We kept creating more and more dashboards while doing ad hoc data pulls for the transportation team. To make things worse, my team had difficulty hiring more data analysts. This caused me to overwork and take on more projects than I would have liked.
A Better Way
Sigma would have been a game-changing tool for our team to use because it would allow the managers to answer their own questions, freeing up our time to focus on other projects. Drilling down into the underlying data is simple and fast with Sigma and managers would be able to create more efficient strategies to improve the supply chain.
We struggled to find the root cause for many of our supply chain issues such as unprocessed orders with our tools. Stakeholders would always ask for multiple dashboards to get a clearer picture of our data. Using Sigma would have saved us time and resources when it came to building out those unnecessary dashboards because we would have access to all the data from one single source of truth instead of combining and exporting CSVs.
Logistics and Supply Chain Analytics with Sigma
Full visibility into your supply chain requires a robust analytics solution that puts billions of rows of live data directly in your hands. Sigma helps teams increase profit margins, mitigate disruptions, forecast demand, and more. Sigma allows organizations to seamlessly expose inventory, product, and shipment data to their external clients.
Let's Sigma together! Schedule a demo today.